Resources for Successful Manufacturing Operations

In the fast-paced world of manufacturing, staying ahead of the competition means capitalizing on every possible advantage. From cutting-edge tools to effective workforce training, a plethora of resources is available to streamline processes, maintain quality, and boost overall efficiency. Deploying these tools effectively can lay the foundation for a robust and resilient manufacturing operation. Below are indispensable insights into achieving operational success in manufacturing. Keep reading to discover how these resources can transform your manufacturing floor into a paragon of efficiency and productivity.
Essential Tools for Streamlined Manufacturing Processes
Efficiency in manufacturing begins with the consolidation of processes and the installation of efficient machinery. With advancements in automation and robotics, tasks that once consumed extensive labor and time can now be completed with precision and swiftness. The application of these tools enhances productivity, delivering a better product at a faster rate, and creating an optimized production cycle that benefits both manufacturers and consumers alike. The GUI includes easy access to Notes and Reminders, allowing users to create, edit, and organize notes, checklists, and tasks. Notes can include text, images, links, and attachments created with anĀ AI text to image generator.
Manufacturers must also prioritize maintenance and diagnostics tools. These not only minimize downtime by predicting equipment failures before they occur but also help in maintaining consistent quality. By integrating sophisticated sensors and diagnostic software, manufacturing enterprises can foresee potential issues, scheduling maintenance proactively rather than reacting to unexpected breakdowns.
Today’s manufacturing landscape also demands adaptability, which is where enterprise resource planning software comes into play. These sophisticated systems allow manufacturers to manage supply chains, inventory, and production schedules with improved accuracy, thereby ensuring that resources are optimally allocated and financial investments yield their maximum potential.
Implementing Quality Control Systems for Manufacturing Excellence
Quality control is paramount in manufacturing, as it directly influences both product integrity and customer satisfaction. Implementing comprehensive quality control systems mitigates the risk of defects and non-compliance with industry standards. Modern quality management software aids in tracking every stage of production, ensuring all products meet predefined specifications before they reach the market.
Manufacturers are increasingly adopting statistical process control (SPC) to monitor and analyze production processes. SPC utilizes statistical methods to identify deviations from the production process, allowing immediate corrective actions. Consistent use of SPC ensures high quality and minimizes variations, leading to more predictable and reliable output.
Quality control also extends to the supply chain, where raw materials and components must meet stringent quality criteria. Building strong relationships with suppliers and conducting regular audits helps ensure that all received materials conform to the necessary quality levels and that any concerns are addressed proactively rather than after production.
Strategies for Workforce Development and Skill Enhancement
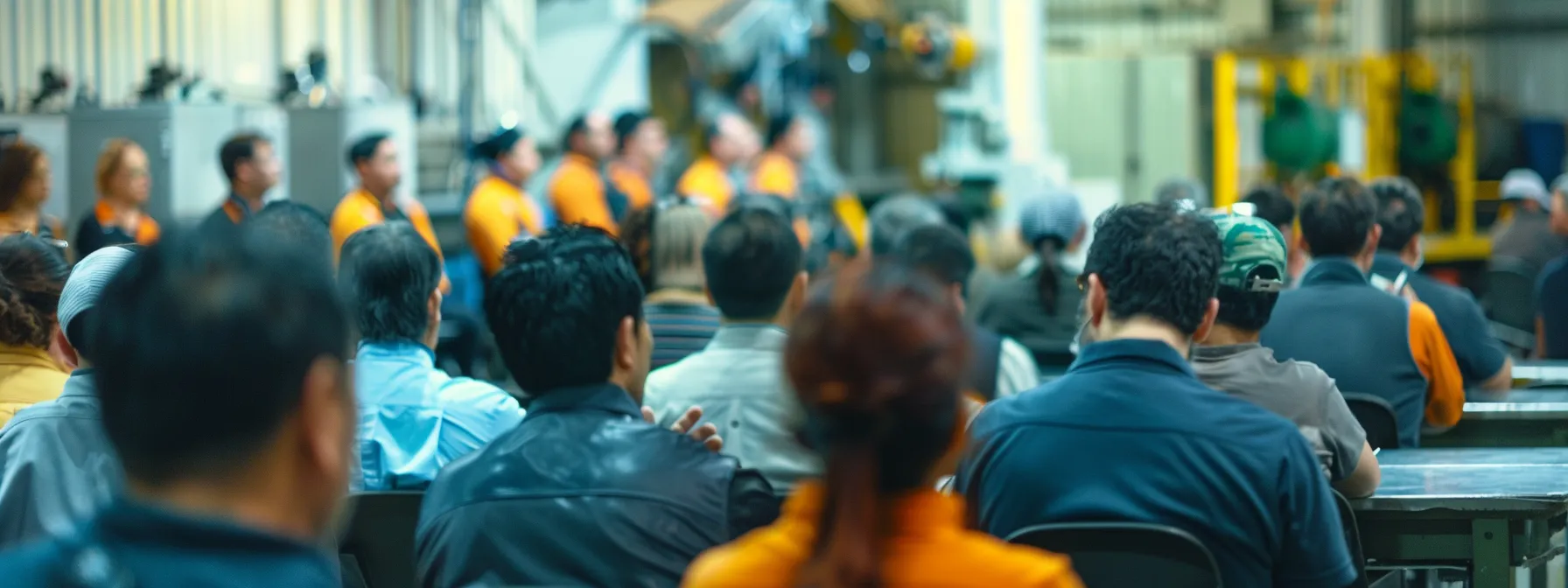
In the manufacturing sector, an experienced and skilled workforce is critical for driving success and innovation. As technology evolves, so too must the skill sets required to operate and maintain new systems. Providing ongoing training and development programs is essential for keeping employees at the forefront of industry advancements.
Manufacturers are investing in apprenticeship and mentorship programs, where less experienced employees benefit from the knowledge of seasoned professionals. These programs are also vital for preserving organizational knowledge, ensuring valuable skills and insights are passed down rather than lost through attrition.
Beyond technical skills, soft skills such as problem-solving, teamwork, and adaptability are increasingly important in today’s manufacturing industry. Workshops and courses that hone these competencies contribute to a more agile and responsive workforce, able to collaborate effectively and adapt to new challenges as they arise.
Sustainable Resource Management in Manufacturing Operations
Sustainability in manufacturing operations is no longer optional but a critical element of modern business practices. Efficient resource management leads to reduced waste, lower costs, and a smaller environmental footprint. Companies that prioritize sustainability often see improved brand reputation and a stronger connection with environmentally conscious consumers.
Manufacturing processes often consume significant amounts of energy and water, so optimizing their usage has become a crucial goal. Through the implementation of energy-efficient machinery and the adoption of renewable energy sources, manufacturers can greatly reduce their operational costs and environmental impact. Similarly, water reclamation and recycling processes can reduce freshwater consumption, benefiting both the ecosystem and the bottom line.
Overall, the successful integration of smart tools, quality control systems, innovative technologies, workforce development, and sustainable resource management form the backbone of a thriving manufacturing operation. Altogether, these components work in synergy to create robust production processes that are both efficient and environmentally considerate, setting the stage for a prosperous future in the manufacturing industry.